
In our CAD model we simply create a disc shaped ‘dummy body’ that fully encapsulates the wheels and tires. In our case setting up a rotating region is relatively easy. A detailed discussion about rotating regions is beyond the scope of this Blog, but there is a good article on the subject here.
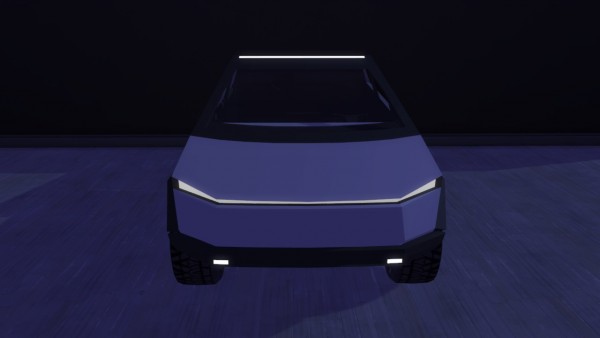
The other method we can use to simulate the flow effects of a rotating wheel is to use a sliding mesh rotating region in SOLIDWORKS Flow Simulation. To highlight this very local flow phenomenon in proximity to the tire boundary layer, we must activate both the ‘Use CAD geometry’ and the ‘Show Boundary Layer’ button on the Cut Plot property manager. The red arrow is pointing to the area of the tire that has a negative X component of velocity. We need to select all the faces attached to the axle of the vehicle.Īs a result of the no-slip condition, air attached to the tires and wheels will now rotate at 71.14 rad/sec, which in the case of the air on the top hemisphere of the tire is opposite to the direction of global air flow! We can study this affect with a cut plot showing X component of velocity through the center of the wheel. We also need to create a local coordinate system centered on each of the wheels to specify the axis about which each wheel is rotating.

In the case of the Tesla Cybertruck, this is 71.14 radians/sec. First, we must calculate the angular velocity (or RPM) of the wheels when the vehicle is moving at 70 mph. This is similar to the Real Wall Boundary Condition from above, but instead of specifying a linear velocity, we specify an angular velocity. The first method is to use a Real Wall Boundary condition, with Wall Motion, on the wheels. There are 2 ways we can do this in SOLIDWORKS Flow Simulation. So, we need to correctly simulate this relative motion between the wheels, the vehicle body and the air in our Virtual Wind Tunnel. In real life the wheels are turning and driving the vehicle forward, creating a local rotating flow near the wheels. We need to consider what is happening to the wheels (and tires). That takes care of the interface between air and ground, but there is one other interface that we need to consider in order to replicate the physics. In our case the Tesla Cybertruck is moving at 70 mph (31.3 m/s), so our inlet velocity is 31.3 m/s and the road also needs to move at this speed in the same direction as the air flow. We do this by setting up a Real Wall Boundary condition, with Wall Motion, in the Boundary Condition property manager, as shown below.
Cybertruck sim software#
Fortunately, SOLIDWORKS Flow Simulation provides an easy way to avoid this all we must do is tell the software that our ground is moving at the same speed as the air. This will create an unwanted boundary layer at this interface which could potentially affect the results. However, if we are not careful with our set-up, and we do nothing more, we will have created relative motion between the air and the ground. This creates the correct relative motion and boundary layer between air and vehicle. In a typical external flow simulation project, we will fix the vehicle in place and then move the air relative to the vehicle using an inlet velocity boundary condition. In flow vernacular, there is no boundary layer at the interface of the air and the road.
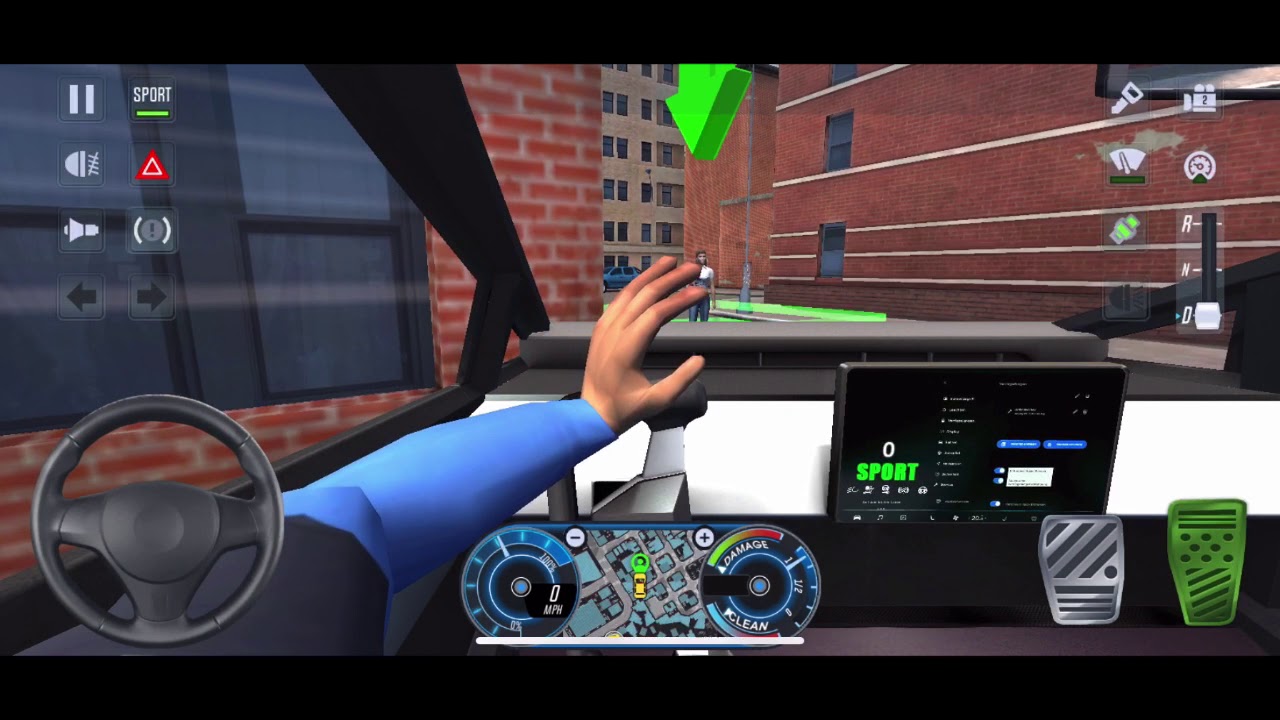
There is relative motion between the vehicle and the road and between the vehicle and the air, but (assuming a windless day) there is no relative motion between the air and the road. In real life, a vehicle moves down a road and creates drag. Luckily, SOLIDWORKS Flow Simulation makes the set-up easy. Fortunately, CFD has largely replaced this expensive process, but care is required to ensure accurate replication of the physics of vehicle flow. This is a very costly exercise wind tunnel time is very expensive, as are the costs associated with constructing the scale models and hiring technicians to run the tests and crunch the numbers. They would build scale models of candidate shapes and measure the drag of these candidates in the wind tunnel. In part 2, I am going to demonstrate some of the nuances for correctly setting up a “Virtual Wind Tunnel” in SOLIDWORKS Flow Simulation.īefore the widespread adoption of Computational Fluid Dynamics (CFD), engineers who sought to explore the aerodynamics of different vehicle shapes would typically book testing time at a wind tunnel facility.
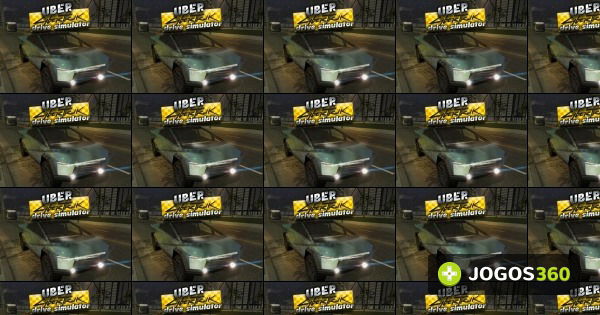
In part 1 of this Blog article I investigated the drag characteristics of the Tesla Cybertruck and explored how symmetry boundary conditions can be used to speed up a flow analysis project in SOLIDWORKS Flow Simulation.
